Pentair Haffmans, in cooperation with a world-leading soft drink producer, developed anew standard in gas filtration featuring a five-stage carbon dioxide (CO2)filter system with anintegrated control and monitoring system.
The CO2 used in soft drink production must meet the highest quality requirements and is subject to strict quality control. To prevent contamination of the CO2 as it moves from the CO2 storage tanks to the mixer, Pentair Haffmans provides a five stage filter combination of coalescence, activated carbon and sterile filters that remove any oils, particles, hydrogen sulfides, aromatic hydrocarbons, or carbonyl sulfides (COS) present in the CO2.
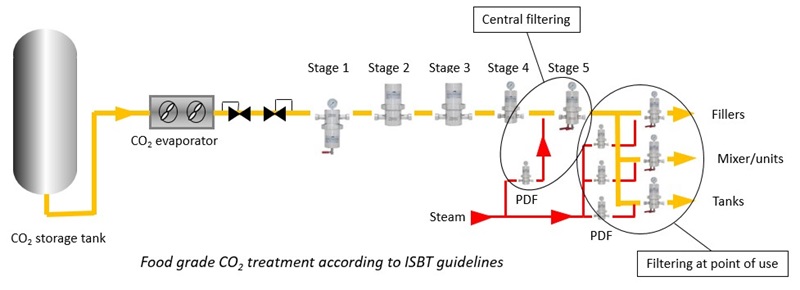
Automation Provides Highest Process Safety
The safety provided by filter systems can be compromised due to the fact that many soft drink producers simply follow manufacturer’s instructions on when to replace the filter elements, which in many cases does not correspond with the actual wear. To assure higher product safety,
Pentair Haffmans automated this process through a control and monitoring system.
The existing filter system was extended with a High-Flow Activated Carbon Filter. To prevent any overload of the filter, an integrated measuring and control system with a flow meter regulates the maximum filter capacity according to specifications. The actual flow rate through the activated carbon filter plus the total flow since the last filter element change, along with a day counter are displayed on a monitor.